|
Documents du débat
Le dossier du maître d'ouvrage
Le dossier du maître d’ouvrage aborde les grands champs du sujet qui structurent le débat.
Dossier du Maître d'ouvrage - Partie 1
Le maître d'ouvrage
Les procédés de fabrication
Les nanotechnologies couvrent des domaines d’application très variés et à chacun sont associés des procédés spécifiques. On peut distinguer la fabrication des nanoparticules utilisées comme renforts dans des matériaux existant par ailleurs (métaux, polymères, céramiques) et les procédés de la nanoélectronique, mis en œuvre pour la fabrication des nanocomposants et nanosystèmes intégrés dans les dispositifs des technologies de l’information et de la communication (TIC).
L’élaboration des nanoparticules
Il existe trois grandes classes de procédés de fabrication de nanopoudres : les procédés physiques, chimiques et mécaniques. Ils visent à faire « germer » l’espèce chimique que l’on souhaite obtenir, puis à en limiter la croissance à la taille que l’on souhaite obtenir ou en contrôler la forme. Ces poudres sont ensuite soumises à des procédés de conditionnement visant à empêcher toute dispersion et à garantir leur innocuité avant leur incorporation dans des matrices pour obtenir des objets. Enfin, les procédés de consolidation visent à obtenir des pièces intégrées dans des systèmes ou utilisées comme telles.
Ces procédés se distinguent également par leur capacité de production. Certains sont déjà très largement utilisés dans l’industrie ; d’autres sont spécifiques aux activités de laboratoire.
Les méthodes physiques de fabrication des nanoparticules font toujours intervenir le changement d’état vapeur-liquide en phase saturée en atomes ou en ions métalliques, suivi d’une trempe rapide à partir de ces états. La condensation brutale de la vapeur métastable dans un gaz inerte (généralement l’argon) favorise la germination de très petits agrégats dont la croissance est à l’origine de la production de poudres ultrafines. La vitesse de refroidissement et la densité de la sursaturation locale influencent la finesse des poudres obtenues.
Dans les procédés chimiques d’élaboration des nanoparticules, une réaction utilisant des réactifs appropriés favorise la germination, limite au maximum la croissance des grains et peut modifier la géométrie, voire la nature des produits formés.
Les méthodes mécaniques, issues directement de procédés bien maîtrisés pour des matériaux classiques, sont probablement celles qui sont le plus utilisées et qui conduisent aux plus fortes productivités (plusieurs tonnes / heure). Elles sont connues sous le terme générique de « mécanosynthèse », réactive (c’est-à-dire accompagnée de réactions chimiques modifiant la nature de la poudre) ou non.
Après avoir été produites, les nanopoudres doivent être conditionnées. En effet, elles sont très pulvérulentes et présentent la propriété d’occuper spontanément l’espace disponible et, de façon antagoniste (mais non contradictoire), en raison de leur forte énergie de surface, elles ont spontanément tendance à s’agglomérer. Il convient également de prévenir les risques d’explosion, toujours très présents en raison de la forte réactivité de surface des nanoparticules. Les nanopoudres sont donc méticuleusement stockées.
Une fois produites, les nanopoudres doivent être consolidées pour réaliser des objets. Diverses méthodes sont disponibles, dont le frittage classique, mais qui, en général, en raison des hautes températures associées à la compression, détruisent une bonne partie de la structure nanométrique. Des méthodes associant compaction et activation par plasma ou encore compression et décharge électrique sont les plus utilisés et conduisent à des pièces qui peuvent être « proches des cotes » et utilisées moyennant un très léger usinage final.
Les procédés physiques d’élaboration des nanoparticules
Les procédés physiques se distinguent par la technique utilisée pour
vaporiser le matériau que l’on souhaite obtenir sous forme
nanoparticulaire. On trouve ainsi :
* l’évaporation-condensation sous pression partielle inerte ou
réactive. Elle permet d’obtenir en condition industrielle (plusieurs
dizaines de tonnes par an) des nanoparticules métalliques ou
céramiques. Cette méthode consiste à évaporer un métal par chauffage
puis à condenser la vapeur métallique afin d’obtenir une poudre de
taille nanométrique. Les conditions opératoires, le recours à une
atmosphère réactive ou non, dépendent beaucoup de la nature chimique
des poudres fabriquées. Ainsi, en atmosphère oxydante on peut obtenir,
en particulier, des nanopoudres d’oxydes métalliques ;
* la pyrolyse laser. La pyrolyse laser
repose sur l’interaction en jets croisés entre l’émission d’un laser
CO2 et un flux de réactifs. Selon les mélanges de précurseurs
introduits dans le réacteur, une grande variété de poudres peut être
synthétisée, telles Si, SiC, SiCN, Si3N4, TiO2 etc. Bien qu’encore
limité aux activités de recherche (avec une productivité de l’ordre du
kg/h), ce procédé pourrait se développer industriellement très
rapidement ;
* les flammes de combustion. La synthèse des nanoparticules est obtenue
par oxydation dans des flammes à partir de précurseurs gazeux ou
liquides. Cette technologie est très utilisée industriellement, en
particulier pour la production de dioxyde de titane (TiO2) utilisée en
cosmétologie ;
* le plasma thermique. Le matériau d’apport est vaporisé dans les
hautes températures produites par un plasma. Les vapeurs produites sont
ensuite condensées sous l’effet d’un refroidissement très rapide
suivant l’étape de fusion-vaporisation. Ce procédé est bien adapté aux
matériaux réfractaires. Il permet de produire des nanopoudres de TiC,
SiC, pérovskites que l’on aurait du mal à synthétiser autrement ;
* le dépôt physique en phase vapeur. Cette technique sous vide (appelée
PVD pour Physical Vapor Deposition), qui consiste à pulvériser une
cible métallique solide, permet de déposer des couches d’épaisseur
nanométrique sur des substrats que l’on souhaite revêtir. Des dépôts de
TiN, CrN, (Ti,Al)N ont ainsi pu être obtenus par PVD cathodique
magnétron, évaporation par arc ou dépôt ionique ;
* les autres procédés. D’autres technologies sont utilisées pour la
production de nanopoudres à l’échelle du laboratoire. On peut citer par
exemple l’utilisation des fluides supercritiques (sans réaction
chimique), les micro-ondes, l’irradiation ionique ou électronique. Ces
procédés en développement ne sont pas utilisés de façon significative à
l’échelle industrielle.
|
Pilote de synthèse par pyrolyse laser du CEA. (détail du réacteur et vue d’ensemble)
Nouvelle machine SPS installée sur la plate-forme de la société Mécachrome à Vibraye (Sarthe). Caractéristiques maximales : force : 2 000 kN ; courant : jusqu’à 30 000 ampères sous une tension de 10V ; température 2 400 °C ; diamètre maximum de pièces réalisables : 350 mm. (équipement opéré en partenariat avec le CEA).
Les procédés chimiques d’élaboration des nanoparticules
Quelques considérations générales s’appliquent à ces procédés chimiques
: la synthèse peut s’opérer en phase solide, liquide ou gazeuse ; les
synthèses en phase liquide ou solide demandent des quantités
importantes de réactifs et de produits ; enfin, en phase gazeuse, la
production de nanopoudres est faible et dispersée dans un grand volume
de gaz. Les grandes productivités sont donc difficiles à atteindre.
Les procédés chimiques sont les suivants :
* les réactions en phase vapeur. Le procédé CVD (Chemical Vapor
Deposition) repose sur une réaction chimique entre un composé volatil
du matériau à déposer et la surface du substrat à recouvrir. Elle peut
être activée par un chauffage du substrat (CVD thermique) ou par
l’action d’un plasma électrique (CVD assistée plasma). Le procédé est
mis en œuvre dans une chambre de dépôt, généralement sous pression
réduite.
Cette technique permet d’élaborer des couches minces de matériaux de
natures très diverses (carbures, nitrures, oxydes, alliages
métalliques, etc.). Elle permet également la synthèse de masse de
nano-objets tels que des nanotubes de carbone ;
* les réactions en milieu liquide. La synthèse en milieu liquide est
réalisée à partir de la mise en solution de réactifs qui vont conduire
à la formation des nanoparticules, dont la taille est contrôlée par
l’utilisation de surfactants ou en réalisant la réaction à l’intérieur
de nanoréacteurs. Ce procédé permet d’obtenir des quantités
industrielles de nanopoudres ;
* les techniques sol-gel. Elles permettent de produire en conditions
industrielles des nanomatériaux à partir de solutions d’alkoxydes ou de
solutions colloïdales. Les matériaux sont élaborés sous forme de
monolithes, de nanopigments cristallisés ou de couches minces. Ce sont
des techniques fondées sur des réactions de polymérisation
inorganiques. Les techniques sol-gel sont utilisées dans de nombreux
domaines : optique, magnétique, électronique, supraconducteurs à haute
température, catalyseurs, et plus particulièrement céramiques
inorganiques et matériaux en verre, matériaux amorphes et
nanostructurés, oxydes multicomposés ;
* les réactions en milieu solide. De nombreux procédés de synthèse
reposent sur les transformations à l’état solide, comme l’obtention
d’oxydes mixtes à partir de poudres (nanométriques) des oxydes purs
correspondant (Y2Ti2O7 à partir d’Y2O3 et Ti02), ou bien par réaction
sur des sites spécifiques, comme Fe2O3 au sein d’une matrice polymère.
Tous ces procédés sont toutefois peu productifs et ne permettent
d’obtenir que des quantités limitées de produits. Ils sont donc
aujourd’hui limités aux activités de développement ;
* les fluides supercritiques avec réaction chimique. Les procédés
utilisant les fluides supercritiques (CO2 ou eau avec réaction
chimique) permettent d’ajuster continûment les propriétés
physico-chimiques du milieu réactionnel sur une grande échelle par
ajustement des paramètres pression et température sur de petites
échelles. La maîtrise des propriétés physico-chimiques du milieu permet
alors de contrôler la réaction chimique et ainsi l’élaboration du
matériau. Ces procédés permettent la synthèse de matériaux inorganiques
finement divisés, comme les métaux, les oxydes et les nitrures.
Néanmoins, leur faible productivité les cantonne actuellement aux
activités de développement. |
Les procédés mécaniques de fabrication des nanoparticules (la mécanosynthèse)
La mécanosynthèse consiste à broyer des poudres micrométriques (1 à 50
μm) de plusieurs alliages. Elles sont introduites dans un conteneur
scellé, agité fortement en présence de billes en acier ou en tungstène
dont le mouvement accroît l’énergie du système. La matière est alors
affinée en continu jusqu’à l’obtention de la taille nanométrique
désirée. C’est selon ce type de procédés que sont produits les alliages
dits ODS (Oxydes Dispersed Strenthening), constitués d’une dispersion
nanométrique homogène d’oxydes dans une matrice métallique (déjà
utilisés dans les applications transport et énergie). L’intérêt de
cette technologie consiste à permettre l’élaboration de matériaux
nanostructurés ou nanorenforcés sans recours à la manipulation de
nanopoudres.
|
Deux grandes voies de conditionnement des nanoparticules
Il existe deux grandes voies de conditionnement : le conditionnement en
phase liquide et l’agglomération en granules micrométriques. La
première vise à mettre en suspension les nanopoudres dans des solutions
de natures diverses (eau, alcool, solvant, polymères ou des polymères
visqueux) mais dépendant des transformations ultérieures.
La seconde consiste à former des agglomérats à partir d’une
transformation à l’état solide comme l’atomisation-séchage (séchage de
suspensions) ou la granulation par trempe rapide (freeze-granulation).
Dans les deux cas on obtient un milieu sécurisé du point de vue
sanitaire et environnemental qui doit être redivisé à l’échelle
nanométrique avant transformation en objets finals pour ne pas perdre
les avantages de la nanostructuration.
|
La fabrication des nanocomposants et nanosystèmes
Les nanocomposants et nanosystèmes recouvrent un champ très important de produits et d’applications : « puces » électroniques, MEMS et NEMS (Micro/Nano Electro Mechanical Systems) qui peuvent être des capteurs de température, de pression, inertiels, etc., des imageurs, des cellules solaires, des têtes de lecture magnétique, des disques durs, des écrans plats LCD (Liquid Crystals Display)…
Tous ces composants se caractérisent par l’utilisation de technologies nanométriques pour leur réalisation, mais le produit final est un produit macroscopique. Celui-ci peut faire quelques millimètres carrés ou centimètres carrés pour les puces électroniques, les MEMS et NEMS ou les capteurs d’image (appareils de photographie numérique) jusqu’à des mètres carrés pour des panneaux solaires ou des écrans LCD.
Ces produits se caractérisent par des procédés de fabrication développés depuis plusieurs dizaines d’années et dont les performances et la précision se sont affinées au cours des ans, de dimensions millimétriques ou submillimétriques dans les années soixante, à des dimensions micrométriques dans les années quatre-vingt, puis submicrométriques à nanométriques dans les années quatre-vingt-dix à deux mille. Au-delà du changement d’échelle, les procédés industriels sont restés fondamentalement les mêmes.
Ces opérations se font dans des salles propres appelées salles blanches dont les niveaux de contamination chimique et particulaire contrôlée sont extrêmement bas pour éviter toute contamination des substrats.
|
|
Exemple de circuit nanoélectronique comportant plusieurs dizaines de millions de transistors
|
Plaquette de silicium de 300 mm réalisée à l’usine STMicroelectronics
de Crolles (Isère) |
|
|
|
|
|
|
|
|
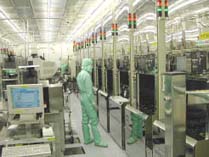 |
|
Salle blanche pour la fabrication de circuits nanoélectroniques. |
Les procédés de fabrication des nanocomposants
Les procédés utilisés pour fabriquer les nanocomposants consistent à
venir insérer un motif fonctionnel sur ou dans un substrat initial. Il
peut s’agir aujourd’hui d’une plaquette de silicium d’un diamètre de
200 mm à 300 mm (figure 4) ou d’un autre semi-conducteur, d’un substrat
de verre ou de plastique, ou même d’un substrat métallique. Les
procédés sont les suivants :
* Modifications locales de composition en utilisant des techniques
d’épitaxie, de diffusion ou d’implantation d’éléments chimiques à des
concentrations extrêmement faibles, inférieures à 1 ppm (partie par
million).
L’épitaxie consiste à faire croître une couche généralement
monocristalline de composition parfaitement définie de quelques
nanomètres à quelques centaines de nanomètres d’épaisseur sur le
substrat, de façon à obtenir de nouvelles propriétés semi-conductrices.
Les procédés utilisés sont généralement la MOCVD (Metal Organic
Chemical Vapour Deposition) qui est un dépôt sous vide en phase vapeur
utilisant des composés organométalliques, ou l’épitaxie par jets
moléculaires (MBE) qui est un dépôt sous vide poussé à partir d’une ou
plusieurs sources solides chauffées.
La diffusion consiste à faire diffuser dans un four à haute température
(à environ 1 000 °C) un composé chimique dans la plaquette de
semi-conducteur.
L’implantation se fait sous vide. Un équipement d’implantation ionique
se compose d’une source de production d’ions, d’un accélérateur de
particules et d’une chambre où se trouvent les substrats ;
* Oxydation ou dépôts de couches de composition et d’épaisseur
extrêmement bien définies : dépôts de couches inorganiques ou de
polymères à partir de solutions, dépôts PVD, CVD ou PECVD tels que
décrits dans le chapitre précédent, ainsi que des méthodes dérivées
encore plus précises telles que la MOCVD ou l’ALD (Atomic Layer
Deposition). Les épaisseurs de ces couches peuvent aller de quelques
nanomètres à quelques micromètres. Jusqu’à très récemment, les couches
déposées étaient de l’oxyde de silicium, des borophosphosilicates, de
l’aluminium, du cuivre, du titane, de l’or, du platine et du nitrure de
titane. De nouveaux composés apparaissent aujourd’hui pour améliorer
les performances électriques ou électroniques des composants, tels que
les oxydes d’hafnium ;
* photolithographie et gravure pour définir des motifs. Ce procédé
permet d’atteindre aujourd’hui des dimensions de motifs extrêmement
réduites de quelques dizaines de nanomètres et donc de mettre sur une
seule puce électronique d’un centimètre carré de surface des centaines
de millions de transistors ;
* photolithographie. Elle utilise des équipements d’exposition sous
rayonnement UV (λ = 365 nm, 248 nm ou 193 nm) dont le principe est le
même que celui des chambres d’exposition photographique classiques, la
longueur d’onde étant simplement plus basse et la résolution meilleure,
puisqu’on atteint aujourd’hui des résolutions de 40 nm (dimension
minimale d’un motif). Pour descendre encore plus bas en résolution
(10-20 nm), sont actuellement développés des équipements à source dite
« Deep UV », de longueur d’onde de 13,5 nm.
* Il existe deux types de procédés de gravure : les procédés de gravure
humide qui utilisent des solutions chimiques pour graver les couches
déposées et les procédés de gravure par plasma, réactif ou non, qui
utilisent une décharge dans un milieu gazeux pour attaquer ces couches ;
* autres procédés : à ces procédés s’ajoutent des recuits thermiques ou
sous flux lumineux, laser ou autres, des procédés de polissage
mécanique ou mécano-chimique et éventuellement d’autres procédés très
spécifiques pour certaines applications. |
|